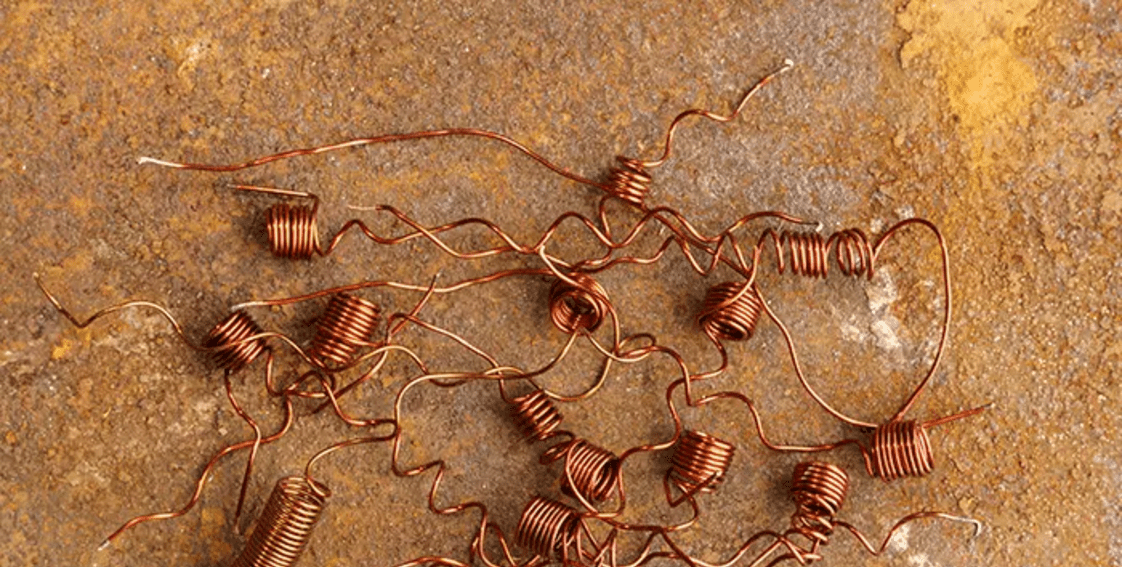
Understanding Custom Wire Form Prototyping
Wire Form Prototyping
- What Happens During Prototyping?
- Design Challenges
- Adapting Designs for Production & Ensuring Accuracy
- Build Custom Wire Forms Prototypes
Prototyping is an important part of any manufacturing process, including CNC bending and wire forming. This process phase not only helps identify potential issues early on, such as structural weaknesses or design inefficiencies but also provides opportunities for improvements, enhancing the reliability and performance of the wire forms in their intended applications.
What Happens During Prototyping?
During prototyping, several things happen:
- Designs are translated. You always start with theoretical designs, then you build them into models to see how they function in a real-world application.
- Materials are tested to evaluate performance under expected conditions, such as stress, temperature, and corrosion. Since wire forms often meet stringent operational standards, it’s critical that the correct materials are chosen.
- Prototypes are subjected to varying conditions in what’s called “functionality testing.” This type of testing can include stress tests, fatigue tests, and load-bearing tests. The primary goal is to ensure the wire form can handle its intended application without failing.
- Measurements are meticulously checked against design specifications to ensure exact dimensional accuracy, making adjustments as necessary. Tools like calipers, micrometers, and CMMs are typically used to take measurements.
- Prototypes are changed after testing, verifying dimensional accuracy, and getting any necessary client feedback. This phase is called “iterative feedback and refinement.” With each iteration, the design is improved, flaws are addressed, and functionality is improved.
Design Challenges
Designing custom wire forms can be challenging, largely due to their diverse applications in the automotive, aerospace, medical, construction, and electronics sectors. Each sector has unique requirements that manufacturers must follow.
Wire forms can also range from simple shapes while others require multiple bends, loops, or coils with precise angles and dimensions. Advanced designs might integrate movement or flexibility in specific areas while maintaining rigidity elsewhere. Creating these complex designs requires highly skilled engineers and sophisticated design software. Additionally, the design often dictates what type of process can and should be used (forming, bending, coiling, welding, etc.).
As mentioned earlier, material selection is also a design challenge, especially because many materials can be used in wire bending/wire forming. Different materials offer varying strengths, flexibilities, resistances to environmental factors like corrosion or temperature, and different degrees of springback, which must be carefully calculated before production.
The diameter of the wire can also pose challenges-thicker wires require more force and may not achieve the same tight radii as thinner wires. In contrast, thinner wires might not have the necessary structural integrity for certain applications.
Lastly, many wire forms are part of larger assemblies. Manufacturers must consider how each wire form will interact with other components, including fit and function, ease of assembly, and potential stresses. Misalignment or improper integration can lead to mechanical failures and other inefficiencies.
Adapting Designs for Production & Ensuring Accuracy

Designs must be accurate before moving forward to full-scale production because CNC wire bending machines follow programmed paths to achieve the correct angles and curves. These machines need exact coordinates and careful programming, as even minor deviations can lead to significant discrepancies in the final product.
As we covered earlier, physical prototypes are built and tested to ensure design accuracy. Many manufacturers use simulation software to predict how the wire will behave during bending, potentially identifying issues with springback, stress points, and interference in complex assemblies.
However, even with the most accurate design and careful testing, some issues could still pop up during wire forming that could impact the final product. CNC machines and other tools, for example, may not be calibrated. Regular calibration ensures that machines and tools operate within their specified tolerances.
Manufacturers ensure accuracy during production by calibrating their equipment, integrating real-time monitoring software to immediately alert operators if the machine deviates from set parameters, and conducting in-line inspections via vision cameras and laser measuring devices to continuously check and verify dimensional accuracy against digital models.
Build Your Custom Wire Forms Prototype With Help From King Steel Fasteners
King Steel Fasteners is an industry-leading supplier of hog rings and other fasteners and a manufacturer of custom wire forms.
We can build a wide range of wire forms with our OMCG CNC bender, including V-hooks, S-hooks, sod staples, fabric pins, and struts that are up to 29 inches in length and 0.250 inches wide.
If you need a custom wire form, contact us today to request a project quote. We can build prototypes quickly to ensure you’re getting the right solution.